Industrial Use Risks Investigated
7th February 2024
Geoenvironmental • Specialist Services
Our Client
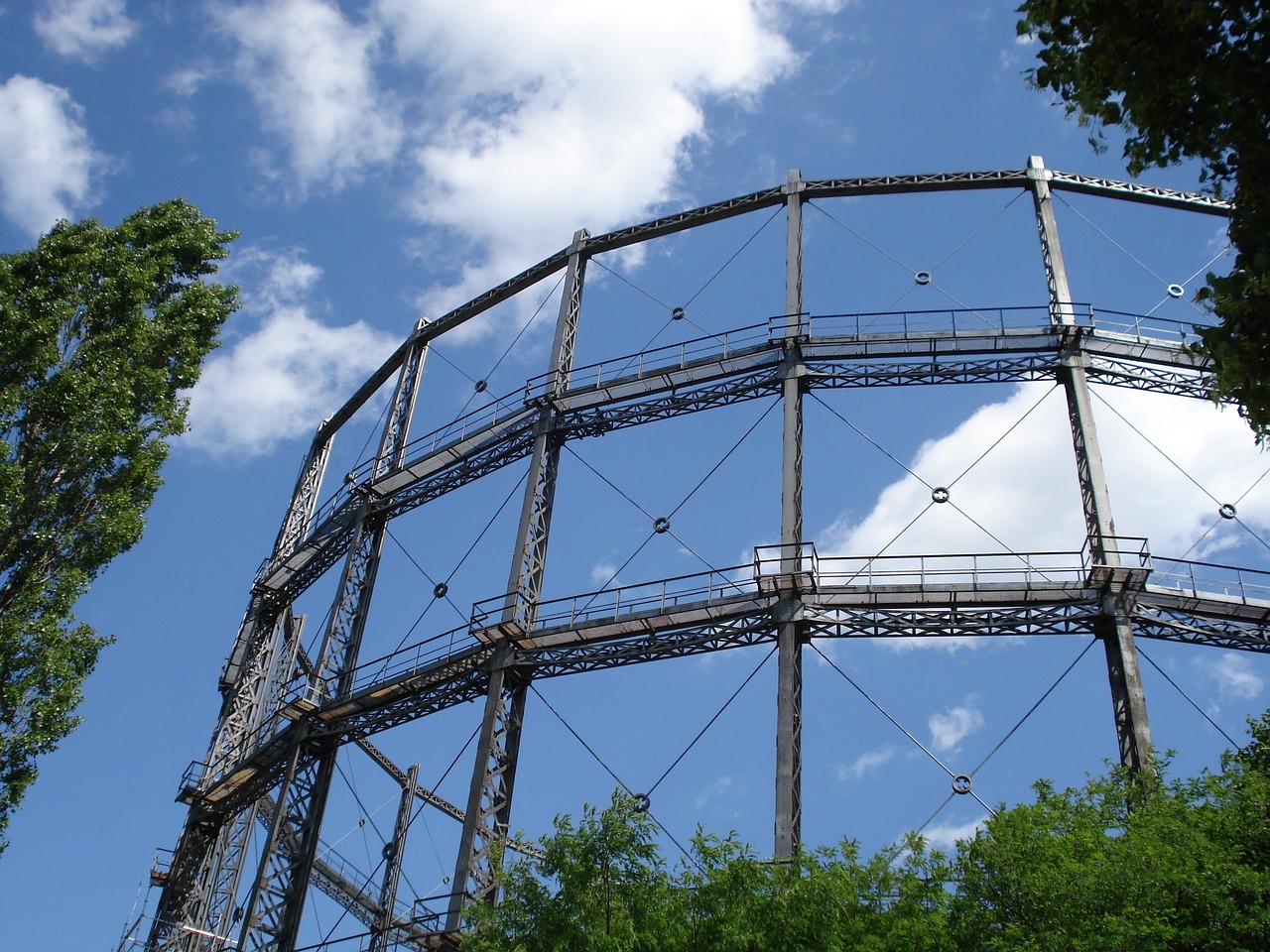
Preliminary-Assessment
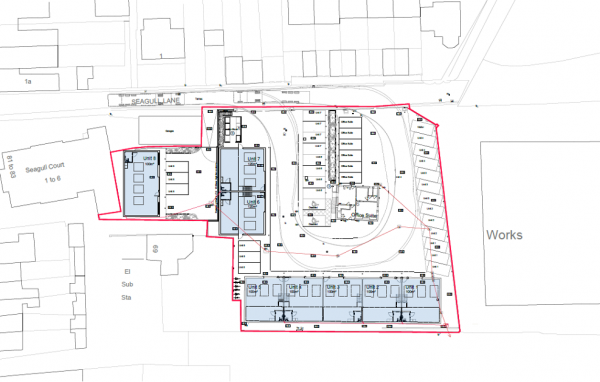
The site comprised a number of former industrial units in varying states of repair. The site was on a gentle west to east slope with the site underlain by Made Ground and River Terrace deposits on the western portion of the site and Made Ground and Head deposits on the eastern portion of the site. The bedrock comprised the London Clay Formation. Alluvial soils were noted on the eastern boundary associated with the River Ems which is located 50m east of the site.
Our Challenge
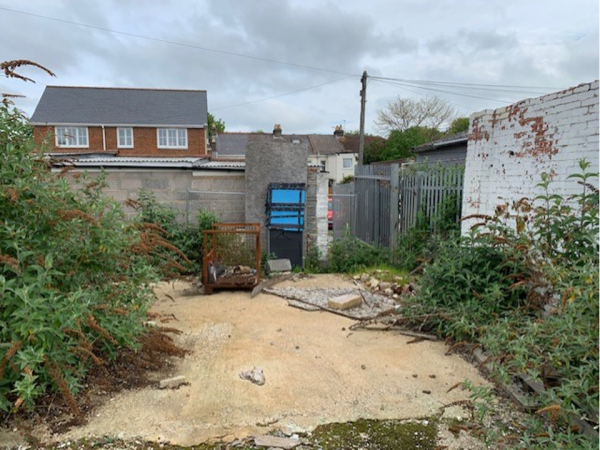
Ground & Water was tasked with investigating the potential risk factors pertaining to the site with reference to former and present day potential contaminative uses, which included former industrial units and a former gas works on site and just to the south of it.
The Ground & Water Approach
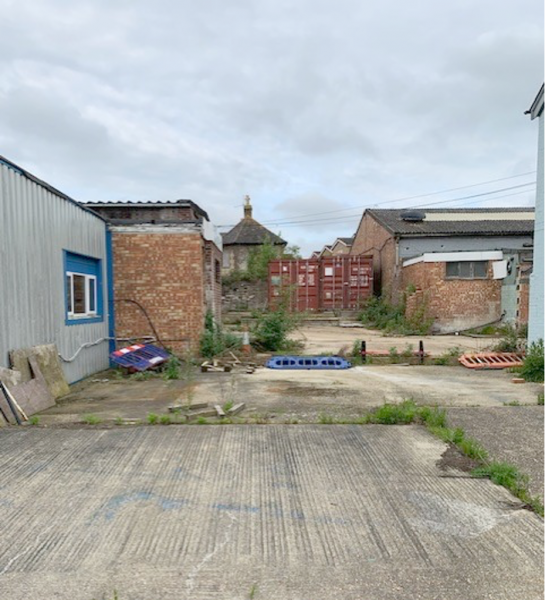
The desk study revealed the site had been used for industrial use since the mid 1970’s. From the earliest mapping records a gas works was recorded on the southern boundary of the site with a large gas holder constructed off site to the south-east by 1896. This gas works was noted until 2010 when it was demolished but the foundations were still visible on aerial photographs. Other off site potential sources of contamination included smithy’s, railway land, Alluvium (gas generating), unspecified tanks, a fire station, electricity sub-stations and works/industrial land.
Phase 2
The intrusive investigation comprised window sampling. Soil samples were obtained and sent for analysis for a broad range of contaminants of concern. Targeted sampling was also undertaken on the south-eastern corner of the site close to the former gas works.
Window sampling was undertaken for the installation of combined groundwater and ground-gas monitoring wells across the site at varying levels. Subsequent gas monitoring was undertaken to assess the gas risk from deep Made Ground on the site as well as gases migrating from the Alluvium to the east.
The drilling and monitoring works noted groundwater levels were particularly high generally above 1.00m bgl. Ground Gas monitoring results recorded very high concentrations of methane during the first monitoring event. However it was noted that the high Groundwater levels were causing a piston effect. Traditional gas monitoring could not be undertaken and therefore Ground & Water proposed gas cannister and water monitoring testing to further investigate the risk to the site.
The results of the further testing indicated that there was a risk from dissolved gases within groundwater to the site based on the high Methane and CO2 concentrations. It was therefore proposed that the site be classified as CS2. Vapour risk to the site was dismissed based off the additional testing results.
The Outcome